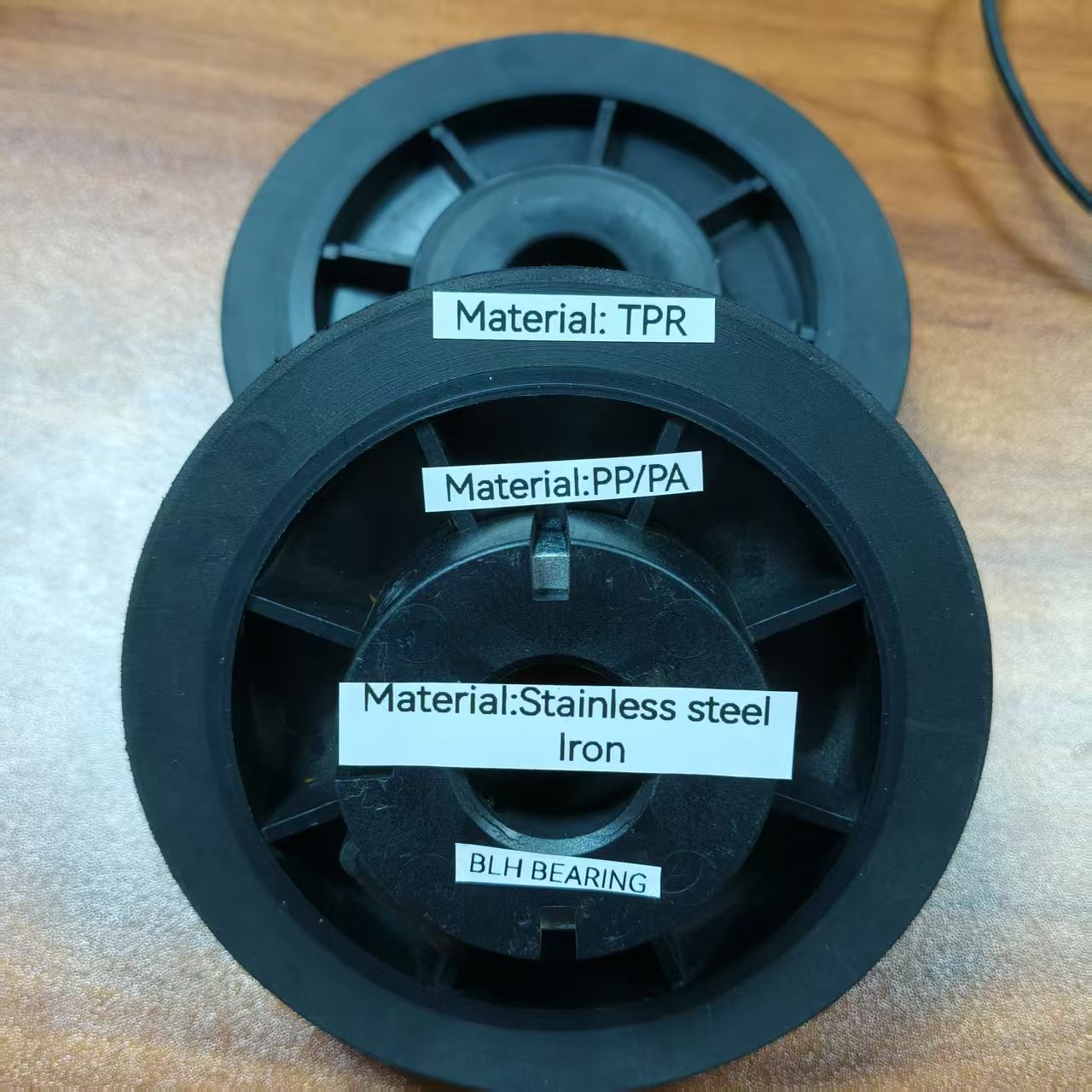
Rollers of Liquid Filling Machines from Chinese Manufacturers: An Excellent Choice with Acid Resistance, Alkali Resistance and High Temperature Resistance
In the field of industrial production, the efficient and stable operation of liquid filling machines is of utmost importance. Among them, the rollers, as key components, directly affect the overall performance of the liquid filling machines. The rollers of liquid filling machines produced by Chinese manufacturers, especially those using rollers with acid resistance, alkali resistance and high temperature resistance, are making a splash in the global market thanks to their excellent quality and performance.
Advantages of Rollers with Acid Resistance, Alkali Resistance and High Temperature Resistance
Adaptability to Harsh Environments
In industrial production, various corrosive liquids and high-temperature environments are often encountered. Rollers with acid resistance, alkali resistance and high temperature resistance can work properly under such harsh conditions, effectively preventing damage caused by corrosion and high temperature, and greatly extending the service life of the rollers. Whether in the chemical, pharmaceutical or food and beverage industries, they can operate reliably.
Ensuring Production Stability
The stable performance of the rollers is the foundation for the continuous and efficient production of liquid filling machines. These rollers made of special materials can maintain stable operation in complex environments, reduce equipment failures and downtime, improve production efficiency, and lower the production costs of enterprises.
Characteristics and Applications of TPR Materials
Introduction to TPR Materials
TPR materials, namely Thermo-Plastic-Rubber materials, are a type of thermoplastic soft rubber materials with rubber elasticity that do not require vulcanization and can be directly processed and formed (such as injection molding, extrusion, blow molding, etc.). It is made by blending and modifying thermoplastic styrene-butadiene rubber (such as SBS, SEBS) as the basic raw material, adding resins (such as PP, PS), fillers, plasticizing oils and other functional additives.
Advantages of TPR in Rollers of Liquid Filling Machines
Good elasticity and wear resistance: TPR materials have the resilience of rubber, which can effectively buffer the vibrations during operation. At the same time, they have good wear resistance and are suitable for the rollers of liquid filling machines that roll frequently, reducing wear and extending the service life.
Excellent anti-slip and shock absorption performance: When the liquid filling machine is running, the TPR rollers can provide reliable anti-slip performance to ensure the stable operation of the equipment. Their excellent shock absorption performance also helps to reduce noise and create a quieter working environment.
Wide operating temperature range: The operating temperature range of TPR materials is -45 ~ 90°C. Generally, TPR materials based on SBS substrates can withstand temperatures of 70 - 75°C. If modified materials based on SEBS substrates are selected, the aging resistance and temperature resistance will be better, and they can better adapt to the possible temperature changes of the liquid filling machine.
Environmental protection characteristics: As an environmentally friendly soft rubber, TPR materials meet the environmental protection testing standards of ROHS, REACH, EN71 - 3, and ASTMF963 in terms of the detection of major hazardous substances such as plasticizers like phthalates, nonylphenol (NP), and polycyclic aromatic hydrocarbons (PAHs), meeting the environmental protection requirements of modern industry.
Characteristics and Applications of EPDM Materials
Introduction to EPDM Materials
EPDM, namely Ethylene-Propylene-Diene Monomer, is a terpolymer of ethylene, propylene and non-conjugated diene. It has excellent weather resistance, ozone resistance, chemical corrosion resistance and good electrical insulation performance.
Advantages of EPDM in Rollers of Liquid Filling Machines
Excellent chemical corrosion resistance: EPDM has a high tolerance to various chemical substances such as acids and alkalis, and can maintain stable performance in a strongly corrosive environment, making it very suitable for the working scenarios of rollers of liquid filling machines in the presence of corrosive liquids.
High temperature resistance: EPDM materials can be used for a long time at relatively high temperatures, and can withstand the heat generated during the operation of the liquid filling machine and the possible high-temperature environment, ensuring that the rollers can still operate normally at high temperatures without deformation or performance degradation.
Aging resistance: It has excellent aging resistance. Even when exposed to harsh environments for a long time, it can maintain good physical properties, reducing the frequency of maintenance and replacement and saving costs for enterprises.
Strengths and Advantages of Chinese Manufacturers
China has many professional manufacturers of rollers for liquid filling machines, equipped with advanced production technologies and equipment. These manufacturers continuously invest in material research and development and process improvement, and can custom-produce high-quality rollers with acid resistance, alkali resistance and high temperature resistance according to the different needs of customers. Whether it is the rollers made of TPR materials or EPDM materials, strict quality standards can be ensured, providing reliable products and high-quality services to customers around the world.
If you are looking for high-performance rollers for liquid filling machines, the rollers with acid resistance, alkali resistance and high temperature resistance from Chinese manufacturers are undoubtedly your best choice. With their excellent performance, reliable quality and reasonable prices, they can meet your various industrial needs and help improve your production efficiency and business development.
I am a Chinese bearing factory capable of solving all technical problems related to bearing transmission. Welcome to contact me at:
jackengineer@blhbearing.com.